Mold Flow Simulation für Druckgussformen
- mkt8280
- 30. Juli 2021
- 2 Min. Lesezeit
Wenn Sie sich zum ersten Mal mit dem Gießen beschäftigen, insbesondere mit dem Druckguss, ist einer der wichtigsten Schritte im Konstruktionsprozess die Formfluss-Simulation. Aber warum führen wir eine Formflussanalyse durch und was ist eine Formflusssimulation?
Wir werden mit diesen beiden Aspekten beginnen und die Gründe und Methoden vorstellen.
Hochdruck-Druckguss-Simulationen
Der Konstrukteur des Druckgussverfahrens ist ein komplexer und empirischer kreativer Job. In der Druckgussproduktion sind die drei Hauptelemente die Druckgussmaschine, die Druckgusslegierung und die Druckgussform. Der Druckgussprozess ist die organische Kombination dieser drei Elemente und die angemessene Wahl der Einstellungen. Deshalb, um Druckguss-Prozess-Parameter für die richtige Auswahl, Kontrolle und Anpassung, so dass eine Vielzahl von Prozess-Parameter, um die Bedürfnisse der Druckguss-Produktion, um zu produzieren qualifizierte Druckguss unter anderen Bedingungen der Qualität.
CAE-Technologie
Nutzung der leistungsstarken Rechen- und Grafikfunktionen von Computern zur Unterstützung der Formkonstruktion, Verbesserung der Konstruktionsgenauigkeit und Konstruktionszuverlässigkeit, Entwurf einer angemessenen Formstruktur und eines angemessenen Gießsystems. Die numerische Simulation des Druckgießprozesses mittels CAE-Technologie, allgemein bekannt als computergestützte Formprüfung, visualisiert den gesamten Prozess des Fließens und Erstarrens der Metallflüssigkeit im Hohlraum während der Gusserzeugung und analysiert die Faktoren der Fehlerbildung.
Mold Flow Simulation und Analyse
Mit der kontinuierlichen Entwicklung von Simulationstechnologie, Computerhardware und -software, den Bedürfnissen des Gießereimarktes, ist die numerische Simulation des Gießprozesses die Erstellung der richtigen mathematischen Modelle, und durch die entsprechenden Werte, verwenden Sie den Computer, um diese Modelle zu analysieren und sie zu verwenden, um die Gießpraxis in Bezug auf die Strömung, Temperatur, Organisation, etc. zu führen.
Die Simulationsergebnisse werden durch Nachbearbeitung beobachtet, und der Strömungs- und Erstarrungsprozess der Metallflüssigkeit im Hohlraum wird durch mehrere Winkel und Profile animiert, um die Ansicht zu verfolgen und die fehlerhaften Teile im Gussteil zu lokalisieren.
Um unsere Kunden bei der Erzielung der besten Produktivität und Teilequalität zu unterstützen, bietet CAMEL stets Fließsimulationen an, bei denen verschiedene Arten von Angussauslegungen entworfen werden. Auf diese Weise liegt unsere T1-Erfolgsquote bei über 96 %.
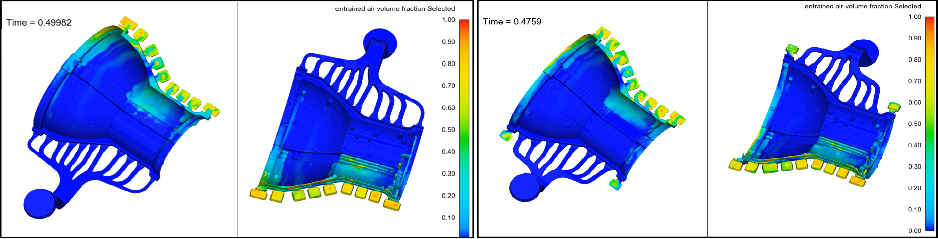
In dieser vorläufigen Fließsimulation zeigt sich, dass die äußersten Speiser kein heißes Metall direkt in die Problembereiche liefern, während der mittlere Bereich gut gefüllt ist. CAMEL passte das Kufenlayout wie unten gezeigt an, um einen erfolgreichen T1 zu erhalten.
Schritt 1: Eliminieren Sie (2) Endspeiser und machen Sie sie überlauffähig.
Schritt 2: Ändern Sie den Speisewinkel und den Anschnitt in Richtung der Außenkante des Teils.
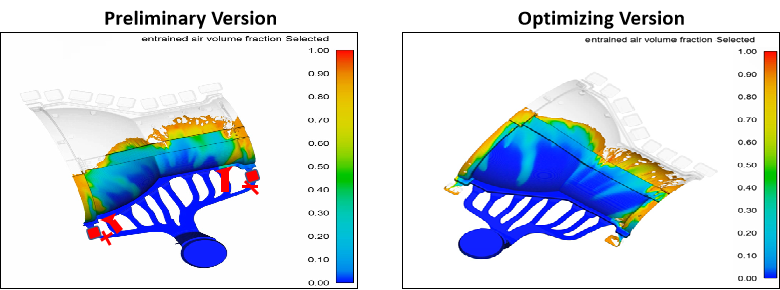
ÜBER DAS KERNGESCHÄFT VON CAMEL:

Fräsen & Drehen
Entwurf & Prototyping
HAUPTBRANCHEN DER KUNDEN:
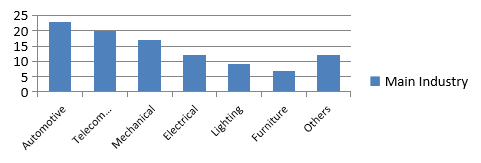
Automobilindustrie
Telekommunikationsausrüstung
Mechanisch
Elektrisch
Beleuchtung
Möbel
Medizinische Instrumente
Comments