Optimierung der Prozessstruktur für Gussteile
- camel-diecasting
- 6. Mai 2021
- 7 Min. Lesezeit
Aktualisiert: 1. Juli 2021
Kurzfassung: Bei der Konstruktion von Druckgussformen wird stärker auf die Aushärtbarkeit der Form selbst, wie Anguss, Überlauf, Temperatur, Auswurf etc. geachtet. Werden jedoch die technologischen Anforderungen der späteren Gussbearbeitung in der Entwurfsphase der Form erhöht sich die Bearbeitungsschwierigkeit des Gussteils.
Die Produktionseffizienz wird reduziert, was sich letztendlich auf die Produktionskosten für die Bearbeitung auswirkt. Daher sollte in der Phase der Werkzeugkonstruktion nicht nur der Druckgussprozess berücksichtigt werden, sondern auch die Anforderungen der anschließenden Bearbeitung sollten stärker berücksichtigt werden, um das Werkzeugkonstruktionsschema effektiv zu optimieren und den wirtschaftlichen Gesamtnutzen von Druckgussteilen zu verbessern. Druckguss hat eine Reihe von Eigenschaften wie hohe Produktionseffizienz, niedrige Kosten, hervorragende Aussehensqualität und lange Lebensdauer der Form.
In der Produktion bestimmt die Rationalität des Formenbaus die Qualität der Gussteile und die Produktionseffizienz. Daher muss der gesamte Formkonstruktionsprozess in Kombination mit den Gusseigenschaften, der Kapazität der Druckgussausrüstung, den verwendeten Materialeigenschaften, den speziellen Kundenanforderungen und anderen relevanten Faktoren vollständig berücksichtigt werden. In der tatsächlichen Produktion jedoch betrachten die meisten Druckgussformkonstrukteure diese Anforderung des Rohlingsdruckgusses als den wichtigsten Entwurfspunkt. Allerdings werden die besonderen Anforderungen der anschließenden Bearbeitung ignoriert, und bei der Bearbeitung von Druckgussrohlingen treten häufig Probleme wie schwierige Positionierung, ungleichmäßige Rohteilaufmaß und verkürzte Werkzeugstandzeiten auf, die die Produktionseffizienz der Bearbeitung und die Stabilität der Gussqualität stark beeinträchtigen und schließlich zum Rückgang des wirtschaftlichen Nutzens der Unternehmen führen. Im Folgenden wird kurz diskutiert, welchen Einfluss die Gefügeeigenschaften von Druckgussformen auf die Zerspanung haben und wie diese optimiert werden können.
1, Einfluss der Anschnittposition auf Schneidwerkzeuge
In vielerlei Hinsicht ist die Einstellung der Angussstelle des Druckgusses der entscheidende und schwierige Punkt bei der Gestaltung des Angusssystems. Jede Nachlässigkeit führt zu unvorhersehbaren Fehlern, die durch die Anpassung des Druckgussverfahrens nicht ausgeglichen werden können. Aus Sicht der Druckgussfertigung sind bei der Auswahl der Angussposition folgende Grundprinzipien zu beachten.
(1) Vermeiden Sie das Schließen des Entlüftungskanals unmittelbar nachdem flüssiges Metall in den Formhohlraum eintritt, was zum Entfernen der Luft aus dem Formhohlraum vorteilhaft ist.
(2) Abzweigstutzen sollten nach Möglichkeit weniger verwendet werden, um sich nicht gegenseitig zu stören und Wirbelströme und Lufteinschlüsse zu bilden.
(3) Die Anschnitte sollten nicht direkt auf den Kern und die Hohlraumwand gerichtet sein, um einen direkten Aufprall von geschmolzenem Metall zu vermeiden.
(4) Die Anschnitte sind an der dickeren Stelle des Gussstücks anzubringen, um die Druckübertragung zu erleichtern.
(5) Der Fluss des geschmolzenen Metalls ist der kürzeste, um den Energieverlust zu reduzieren und eine zu starke Kühlung zu vermeiden.
(6)Die Anschnitte dürfen beim Schrumpfen des Gussstücks keine Verformung verursachen.
(7) Stellen Sie den inneren Anguss so nah an die wichtigen Teile des Werkstücks. Wenn die Einstellung der Anschnittstelle die oben genannten Bedingungen erfüllen kann, ohne die anschließende Bearbeitung des Rohlings zu berücksichtigen, kann die Einstellung der Anschnittstelle als perfekt bezeichnet werden. Allerdings müssen die meisten Druckgussteile in der Produktion bearbeitet werden. Wenn die tatsächliche Nachfrage nach der Bearbeitung von Gussrohlingen ignoriert wird, wird dies definitiv einige unnötige Probleme mit sich bringen. Die wichtigsten Erscheinungsformen sind: der Einfluss der Rückstände nach dem Entfernen des Anschnitts auf die Bearbeitungspositionierung und das intermittierende Schneiden während der Bearbeitung von Angussteilen.
Wie wir alle wissen, ist das intermittierende Schneiden eine technologische Schwierigkeit bei der mechanischen Bearbeitung, die periodische Vibrationen erzeugen kann, Streifen oder Wellen auf der bearbeiteten Oberfläche erscheinen lassen, was zu einer Erhöhung des Oberflächenrauheitswertes führt. Intermittierendes Schneiden im Schneidprozess führt zu einer periodischen Belastung des Werkzeugs, was leicht zum Zusammenbruch des Werkzeugs führt und die Lebensdauer des Werkzeugs verringert. Beim intermittierenden Schneiden muss der Bediener eine geringere Schnittgeschwindigkeitsverteilung und einen kleineren Vorschub verwenden, was die Produktionseffizienz der Maschine und des Arbeiters beeinträchtigt.
Relativ gesehen ist der Einfluss auf die Positionierung geringer. Bei der Konstruktion von Bearbeitungsvorrichtungen sollten mehr Verständnis und Kommunikation erfolgen, um die Angussform und -position des Rohlings zu bestätigen, die ungefähre Größe des Angussrückstands in der Zukunft abzuschätzen und zu vermeiden, die Angussposition als Positionierungs-Benchmark für die Bearbeitung zu verwenden.
Unter der Prämisse, die Druckgussproduktion zu erfüllen, muss die Einstellung der Angussstelle daher auch die technologischen Anforderungen der nachfolgenden Bearbeitung berücksichtigen und die Angussstelle des Rohlings entsprechend dem tatsächlichen technologischen Bearbeitungsprozess angemessen anordnen. Wenn nicht beides möglich ist, wird empfohlen, den Anschnitt auf einer exponierten und flachen Ebene zu platzieren, um das Polieren zu erleichtern und das Aufmaß zu reduzieren. Oder die Anschnittposition und -größe werden gleichmäßig und kontinuierlich auf der Bearbeitungsebene platziert, um intermittierende Schnitte zu reduzieren.
1.Wie in Bild 1 gezeigt, handelt es sich um ein häufiges Problem bei der Auswahl des Angussortes. Bild 1a, dass der Anschnitt auf die bewegliche Matrize gesetzt wird und der Anschnitt in Zukunft auf der Kreisebene bleiben wird. Aus Sicht der Druckgusstechnik ist die Angussgarnitur auf der beweglichen Kokillenseite vorteilhaft für das Einfüllen von Metallschmelzen und die Druckgussherstellung von Gussteilen. Die Anschnittrückstände auf der Kreisebene können jedoch durch nachfolgende Bearbeitung entfernt werden, und das Gussstück hat ein schönes Aussehen und keine Spuren von Anschnittrückständen, aber es bringt das Problem des intermittierenden Schneidens mit sich. Abb. 1b ist an der festen Kokillenseite angesetzt und der Anschnitt verbleibt zukünftig am Umfang des Gussstücks. In Bezug auf das Druckgussverfahren wird die Metallflüssigkeit, die an einem solchen Anguss abgesetzt wird, direkt auf die Hohlraumwand der Form auftreffen, die an den entsprechenden Teilen des Angusses leicht an der Form haften kann. Wenn der Anschnitt in Zukunft entfernt wird, bleiben Anschnittspuren am Umfang des Gussstücks zurück, die das Aussehen des Gussstücks beeinträchtigen. Das Problem des intermittierenden Schneidens wird jedoch vermieden, ohne den Umfangsteil zu bearbeiten.
2. Die Auswahl in der tatsächlichen Produktion muss mit den Merkmalen ihres jeweiligen Unternehmens kombiniert und umfassend mit der Kundennachfrage als Orientierung abgewogen werden. Hervorzuheben ist hier, dass bei der Gestaltung von Druckgusswerkzeugen die Anforderungen der Zerspanung so weit wie möglich berücksichtigt werden sollten.
2.Einfluss der Anschnittposition auf die Bearbeitung Positionierungsbearbeitung
1.Im Allgemeinen sollte für die Positionierung eine Grobreferenz auf dem Rohling gewählt werden, und dann sollte eine Feinreferenzbearbeitung durchgeführt werden. Diese groben Benchmarks erfordern Glätte, Zuverlässigkeit und Konsistenz. Für grobe Benchmarks gibt es hauptsächlich zwei Auswahlmethoden.
(a) Wenn die Maßkette des bearbeiteten Gussmodells keine bestimmte unbearbeitete Oberfläche als Konstruktionsmaßstab verwendet, wird bei der Bestimmung des groben Maßstabs häufig die größte Ebene, der Außenkreis oder die größte Innenbohrung des Rohlings ausgewählt, da diese Funktionen können die maximale Positionierungsgrenze erreichen und die Genauigkeit und Konsistenz der Positionierung sicherstellen.
(b) Wenn die Maßkette auf der bearbeiteten Gusszeichnung eine unbearbeitete Fläche als Konstruktionsbezug annimmt, muss der Grobbezug gewählt werden, da der aus diesem Bezugspunkt bearbeitete Feinbezug die Zeichnung in der nachfolgenden Bearbeitung darstellen kann. Als Prozessbezugswert wird der ursprüngliche Konstruktionsbezug verwendet. Wenn der Anschnitt in diesen Bereichen erscheint, wird die Gussteilpositionierung stark beeinträchtigt. Entsprechend der Bearbeitungspositionierungsmethode sieht das entsprechende Optimierungsschema wie folgt aus:
(1) Die Torposition sollte nach Möglichkeit nicht auf einer größeren Ebene für die Positionierung oder auf einer sehr genauen Konstruktion gewählt werden.
(2) Wenn der Anschnitt zwecks Positionierung oder konstruktionsbedingt auf einer größeren Ebene platziert werden muss, berücksichtigen Sie mehrere Vorschubstränge und reservieren Sie die erforderliche Position für die Positionierung, wie in Abb. 2 gezeigt. Der mittlere Bereich der Strangteilung ist immer noch eine ebene Fläche, die mit anderen Flächen eine Dreipunkt-Ebenen-Positionierung (wie die Außenkreis-Positionierung) bilden kann.
(3) Wenn das Gussteil dies zulässt, fügen Sie Prozesspositionierungsnocken hinzu (siehe Abb. 3), um die Bearbeitungspositionierung des groben Bezugsniveaus zu optimieren.
(a)Der Anguss an der Kernseite (b)Der Anguss an der Hohlraumseite

Bild 1 Unterschiedliche Auslegung von Gate-Position
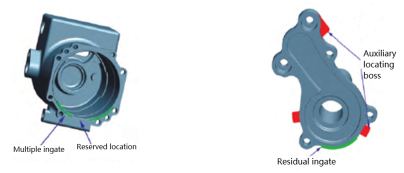
Durch das obige Optimierungsschema kann die Zuverlässigkeit der Positionierung der Gussbearbeitung verbessert werden. Darüber hinaus kann die Berücksichtigung der Verformung am Anguss und die Optimierung des Angussentfernungsprozesses während der Druckgussproduktion die Bearbeitungspositionierung verbessern.
2. Einfluss von reservierten Löchern
1.Einfluss von Reservelöchern auf die Positionstoleranz
Es wird allgemein angenommen, dass das Loch so weit wie möglich für die in der Form umsetzbaren Lochformen reserviert werden sollte, um das Bearbeitungsaufmaß zu reduzieren, die gehärtete Schicht des Gussstücks zu schützen und die gute Luftdichtheit des Gussstücks zu gewährleisten . Die Reservierung von Bodenlöchern wirft jedoch manchmal eine andere Frage auf, ob diese Stiftlöcher die Positionstoleranzanforderungen des Gussteils erfüllen können und die Bearbeitung nicht beeinträchtigen. Wenn nach der Bearbeitung eine Position außerhalb der Toleranz auftritt, ist es sehr wahrscheinlich, dass die Position außerhalb der Toleranz der voreingestellten Bohrung dazu führt, dass das Werkzeug der falschen voreingestellten Bohrung folgt. Die Führung weicht von der voreingestellten Bearbeitungsgröße ab. Die Basis der reservierten Bohrung ist die Fertigungsbasis der Form, und während der Bearbeitung ist die Auswahl der Prozessbasis und der Formenherstellungsbasis nicht konsistent, die reservierte Bohrung muss auch vom Prozess abweichen Basis, so dass es zu einer Position außerhalb der Toleranz führt.
Diese Art von Problem kann auf folgende Weise gelöst werden:
(1) Bei der Gestaltung der Form wird der Benchmark für die Formherstellung so weit wie möglich als grober Positionierungs-Benchmark für die Bearbeitung verwendet. Nach der Vereinheitlichung des Benchmarks wird die Positionsgenauigkeit der Lochbearbeitung verbessert. Zum Beispiel sollte die reservierte Bohrung mit Positionsanforderung gleich der Positionierungsfläche der Prozessreferenz auf der Trennfläche der Werkzeugseite sein, um den Fehlereinfluss der Werkzeugklemmverschiebung zu reduzieren.
(2) Aufgrund der Produktvielfalt ist es manchmal schwierig, die Herstellungsstandards zu vereinheitlichen. Zu diesem Zeitpunkt wird empfohlen, das reservierte Loch mit geringer Bearbeitungstiefe zu löschen.
(3) Die Positionierung und Bearbeitung des Lochs werden durch maschinelle Bearbeitung abgeschlossen, wodurch der Führungseffekt des voreingestellten Bodenlochs eliminiert und die Positionsgenauigkeit verbessert wird. Es sollte jedoch auch beachtet werden, dass ein großer Schnittrand Fehler im Druckguss freilegt.
2.Einfluss der Reservebohrung auf die Bearbeitungspositionierung
In der Zerspanung wird oft das reservierte Loch des Rohlings auf dem Druckgussteil als Grobpositionierung verwendet, daher ist die Zuverlässigkeit des reservierten Bodenlochs für die Positionierung besonders wichtig. Dies ist wichtig, daher wird empfohlen, die Priorität der voreingestellten Lochpositionierung zu berücksichtigen.
(1) Der Kern des reservierten Lochs der Form sollte so weit wie möglich mit dem Kern integriert sein, um die Verwendung eines abnehmbaren separaten Körpers zu vermeiden. Der Hauptgrund ist, dass der geteilte abnehmbare Kern verwendet wird – nach einer gewissen Zeit bilden sich Grate auf der Verbindungsfläche der Stiftlochanordnung, und diese Grate sind sehr dünn und weich. Selbst wenn sie entfernt werden, haftet ein kleiner Teil davon an der Lochwand und beeinträchtigt die Positioniergenauigkeit.
(2) Voreingestellter Lochkern für die Positionierung
Die Neigung der Form wird vergrößert und die Oberflächenhärte wird so weit wie möglich erhöht, damit die Form während der Druckgussherstellung reibungslos gelöst werden kann, die Möglichkeit des Verklebens der Form und des Ziehens der Innenwand des Lochs verringert werden kann, und die Positioniergenauigkeit kann verbessert werden.
(3) Wenn das reservierte Loch mit kleiner Öffnung und geteiltem Typ als grobe Positionierungsreferenz verwendet wird, ist es besser, während der Herstellung der Form mehr Kerne des Lochs vorzubereiten, um die Stabilität und Konsistenz der Lochgröße während der Formwartung sicherzustellen und vermeiden unnötige Verluste für die nachfolgende Bearbeitung. Ob das reservierte Loch geeignet ist oder nicht, beeinflusst die Positionierung und Genauigkeit der Bearbeitung. Daher ist es im Druckgussproduktionsprozess nicht nur darauf zu achten, ob das reservierte Loch verformt ist oder nicht, Schimmelpilze und andere Qualitätszustände zu verkleben, sondern auch die tägliche Kernwartung zu verstärken, um die Konsistenz des Positionierungs-Benchmarks zu gewährleisten .
3. Fazit
Zusammenfassend lässt sich sagen, dass das Formdesign aus Sicht der Gussbearbeitung bequemer zu lokalisieren und die Überschussverteilung angemessener ist, insbesondere sollte der Herstellungsstandard der Form gut mit dem Bearbeitungsprozess übereinstimmen, was zur Verbesserung der Effizienz und Qualität der Bearbeitung. Daher müssen Konstrukteure bei der Konstruktion von Druckgussformen alle Aspekte umfassend berücksichtigen, was neue Anforderungen an die Erweiterung der beruflichen Fähigkeiten von Druckgusskonstrukteuren stellt. Ein exzellenter Druckgussdesigner muss ein technisches Talent mit Formentechnik, Druckgusstechnik und Bearbeitungstechnik sein.
Comments