Optimierung des Druckgussprozesses für die Frontabdeckung von Automobilmotoren aus Aluminiumlegierun
- camel-diecasting
- 6. Mai 2021
- 5 Min. Lesezeit
Aktualisiert: 1. Juli 2021
Mit der rasanten Entwicklung der Automobilindustrie werden aufgrund der Anforderungen an den Karosserieleichtbau zunehmend Leichtmetallwerkstoffe in Teilen und Komponenten eingesetzt. Aluminiumlegierungen (wie Legierungen der Aluminium-Silizium-Reihe) haben die Eigenschaften einer geringen Dichte, eines niedrigen Wärmeausdehnungskoeffizienten und guter Reibungseigenschaften und werden in großem Umfang in Kraftfahrzeugmotorabdeckungen, Getriebegehäusen und anderen Gussteilen verwendet. In diesem Thema wird die Magma-Software verwendet, um den Füll- und Erstarrungsprozess der Frontabdeckung aus einer Aluminiumlegierung eines Familienautomotors zu analysieren; Durch die Analyse der Ergebnisse der numerischen Simulation wird ein Optimierungsplan für den Druckgussprozess vorgeschlagen, der eine Referenz für die Herstellung ähnlicher Produkte bietet.
Gussmodell und Material
1. Casting-Modell
Die Außenabmessungen der Frontabdeckung des Motors betragen ca. 470 mm × 310 mm × 105 mm, die Produktmasse beträgt ca. 3,4 kg, die durchschnittliche Wandstärke des Hauptkörpers beträgt 3,3 mm und die maximale Wandstärke erreicht 26 mm (das Teil im Drahtrahmen ist die dickere Wand markiert) . Die Produktstruktur ist relativ komplex, mit einer beträchtlichen Anzahl von Schraubenlöchern und im Inneren verteilten Verstärkungsrippen; und die Wanddicke des Gussteils ist sehr unterschiedlich, und es ist wahrscheinlich, dass während des Druckgussverfahrens eine Spannungskonzentration auftritt, was zu einer ungleichmäßigen Dichte führt, was zu Gussteilverformung, Schrumpfung und Schrumpfporosität führt. . Das Gussproduktmodell ist in Abbildung 1 dargestellt.
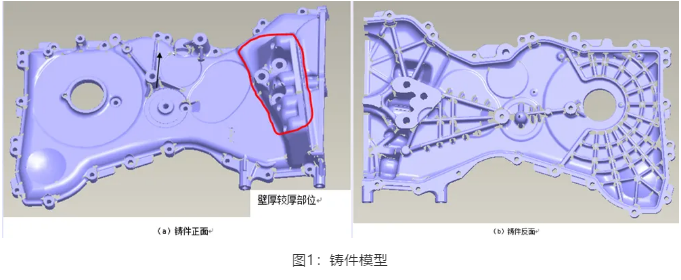
2. Gussmaterialien
Die Frontabdeckung des Motors muss gute mechanische Eigenschaften und eine hohe Dichte aufweisen, und es dürfen keine inneren Defekte wie Risse, Schrumpfporosität, Poren und Schrumpflöcher zugelassen werden. Basierend auf den oben genannten Arbeitsumgebungen und Anforderungen wird die Aluminiumlegierung AlSi9Cu3 ausgewählt, die eine gute Fließfähigkeit und eine hervorragende Druckgussleistung aufweist. Tabelle 1 enthält die chemische Zusammensetzung und die mechanischen Eigenschaften.
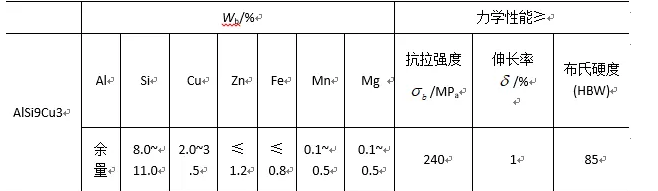
Erster Prozessplan für den Druckguss
1. Design des ersten Gießsystems
Entsprechend den Merkmalen der Produktstruktur ist geplant, 2 Abzweige mit insgesamt 6 Innenkanälen für die Beschickung zu konzipieren, wie in Abbildung 2 dargestellt 6-Wege-Innentor durch den 2-Wege-Abzweig und gelangt schließlich zum Füllen in die Kavität.
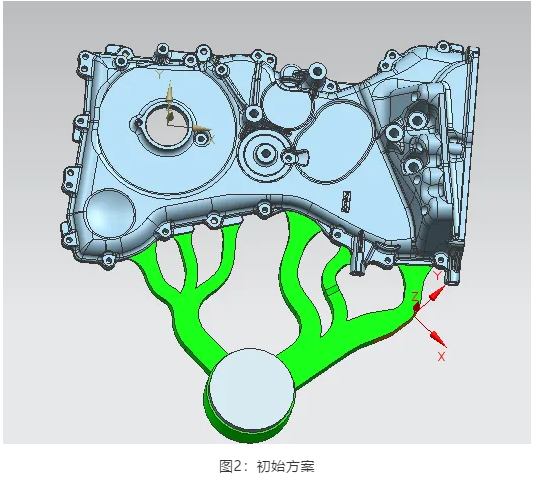
1. Ermittlung von Prozessparametern
Das Gussmaterial ist AlSi9Cu3 und die Form ist DIEVAR. Aufgrund der physikalischen Eigenschaften der beiden Materialien, kombiniert mit dem Konstruktionshandbuch für den Druckgussprozess und der Produktionserfahrung, und durch Berechnungen werden die folgenden Parameter des Druckgussverfahrens bestimmt: Die Anfangstemperatur des Gussteils beträgt 670 °C und die anfängliche Temperatur von Temperatur der Form beträgt 180℃; Die Gießmasse beträgt 3,4 kg, die Masse des Gießsystems beträgt 2 kg, die Masse des Überlaufsystems beträgt 850 g und die Gesamtmasse beträgt 6,25 kg. Die projizierte Fläche des Gussstücks beträgt 1 196 cm2 und die gesamte projizierte Fläche beträgt 1 554 cm2; der spezifische Einspritzdruck wird mit 60 MPa gewählt und der Sicherheitsfaktor beträgt 1,2
2. Simulationsanalyse des vorläufigen Plans
Um das Füllen und Erstarren des Gussstücks während des Gießprozesses zu verstehen, wird die Software Magma zur numerischen Simulation verwendet, wie in Bild 3 dargestellt. Es ist zu erkennen, dass die Füllzeit der gesamten Kavität ca. 0,076 s beträgt. Die anfängliche Füllgeschwindigkeit des in die Kavität eintretenden geschmolzenen Metalls ist schneller, und die Füllgeschwindigkeit des mittleren Bereichs ist deutlich schneller als die der beiden Seiten. In der Mitte des Füllens dringt die Metallschmelze nach und nach in den dickeren Wandbereich ein. Von Zeit zu Zeit wurde beobachtet, dass der dickwandigere Bereich relativ langsam gefüllt wurde und es leicht zu einer Gasstagnation kam. Nach Abschluss des Füllens des Bereichs traten aufgrund höherer Temperatur und längerer Erstarrungszeit anfällig innere Qualitätsprobleme wie Poren und Lunker auf.

Design zur Optimierung des Druckgussprozesses
1. Optimiertes Design des Angusssystems
Angesichts des relativ langsamen Füllens von dickwandigen Bereichen wird vorgeschlagen, um die Qualität der Gussteile zu gewährleisten und die Füllgeschwindigkeit jedes Bereiches während des Umformprozesses im Wesentlichen gleich zu machen, zwei Angusszuführungen zu den dickwandigen ummauerte Bereiche, um die Füllgeschwindigkeit dieses Bereichs zu beschleunigen, was den gesamten Füllprozess stabiler und reibungsloser macht, die Beseitigung von Gas fördert und Schrumpfung, Schrumpfung und andere Fehler vermeidet. Abbildung 4 zeigt das optimierte Schema, und der Drahtrahmenteil ist ein 2-Wege-Gate mit zusätzlichem Vorschub. Da die Angussposition einen großen Abfall von der Unterseite des Gussstücks aufweist, wird hier, wie in Abbildung 5 gezeigt, ein Schieber am Anguss angebracht, um sicherzustellen, dass die Aluminiumflüssigkeit den Bereich ausfüllt, um die Zufuhr dieses Bereichs reibungslos zu gestalten Gut.
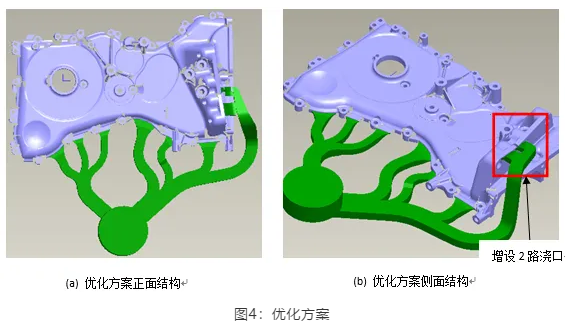

2. Simulationsanalyse des Optimierungsplans
Um den Fülleffekt und die Erstarrung des optimierten Schemas zu überprüfen, wurde erneut eine numerische Simulation durchgeführt, um den Füll- und Erstarrungsprozess des optimierten Schemas zu beobachten. Der Simulationsprozess wird unter den Aspekten Fülltemperaturfeldänderung, Luftdruckänderung, Erstarrungssituation usw. analysiert. Durch Beobachtung wurde festgestellt, dass der gesamte Hohlraumfüllprozess etwa 0,071 s dauert, was der theoretischen Schätzung sehr nahe kommt. Während des Füllvorgangs bewegt sich das geschmolzene Aluminium relativ gleichmäßig und die Geschwindigkeit ist im Wesentlichen gleich; der Gasaustritt in der Kavität ist glatt, der Luftdruck ist relativ stabil und innerhalb des Risikokontrollbereichs gibt es keine offensichtliche Gasstagnation und -mitnahme. Beim Erstarrungsprozess erfolgt die Abkühlung und Erstarrung mit Ausnahme der dickeren Bereiche langsamer und die Erstarrung und Abkühlung anderer Bereiche ist grundsätzlich gleichmäßig und ideal.
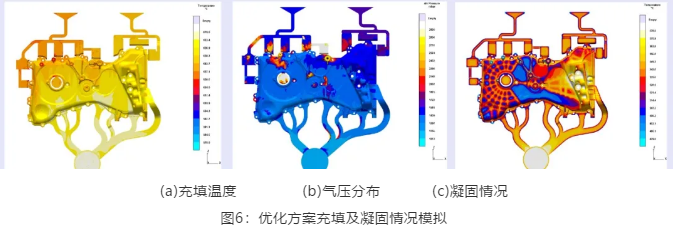
Lokales Kühlschema
1. Hochdruckpunktkühltechnologie
Die Hochdruck-Punktkühlung wird in den letzten Jahren zunehmend in der Druckgussindustrie eingesetzt. Das Kühlwasser wird durch den Hochdruckpunktkühler auf den idealen Druckzustand gebracht und das entsprechende Rohr zur Kühlung schnell durch das Werkzeug geführt. Da die Kernkühlgeschwindigkeit bei diesem Prozess hoch ist, werden keine Schrumpflöcher in der Nähe der Kernposition gebildet. Daher kann der Einsatz der Hochdruck-Punktkühlungstechnologie einen Formwärmeausgleich erreichen, lokale Porenfehler effektiv verbessern, die Lebensdauer der Form erheblich verlängern, die Kernaustausch- und Überholungsrate reduzieren und die Qualität der Gussteile besser garantieren.
2. Hochdruckpunkt kalt im lokalen Bereich
Angesichts des langsamen Abkühlens und Erstarrens des dickeren Teils im numerischen Simulationsanalyseprozess wird die Hochdruckpunktkühlung zur schnellen Kühlung der Schlüsselbereiche zur Sicherstellung der Qualität der Gussteile in Betracht gezogen. Durch die Strukturanalyse von.
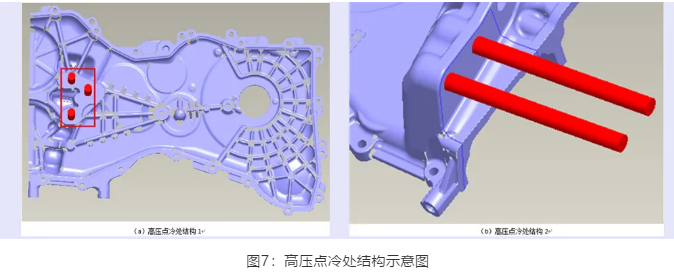
Formenentwicklung und Versuchsproduktion
Nach dem optimierten Prozessplan wurden Druckgussformen entwickelt und eine Probeproduktion durchgeführt. Die Probeproduktion erfolgte auf der Horizontal-Druckgussmaschine DCC1250T. Die Formstruktur ist in Abbildung 8 dargestellt. Die Anfangstemperatur der Probeform beträgt 180 °C. Während des Probeproduktionsprozesses tritt das geschmolzene Aluminium während des Einspritzvorgangs in der Niedriggeschwindigkeits-Injektionsphase durch den Anguss in den Angusskanal ein, tritt dann reibungslos vom inneren Anguss in die Kavität ein und tritt schnell in die Hochgeschwindigkeits-Injektionsphase ein. In Schlüsselbereichen wird eine Hochdruckpunktkühlung durchgeführt, um die Erstarrungszeit jedes Teils des Gussstücks im Wesentlichen konstant zu halten. Abbildung 9 ist ein Foto des Testprodukts. Es ist zu erkennen, dass die Oberfläche des Gussstücks glatt ist, der Umriss klar ist, die Qualität des Innenlochs gut ist und keine offensichtlichen Mängel vorhanden sind. Das Produkt wurde auf Luftdichtheit und mechanische Eigenschaften getestet. Nach der Inspektion hat die Erfolgsquote des Produkts 96% erreicht und die Testergebnisse erfüllen die Leistungsanforderungen.

Abschließend
(1) Unter Verwendung der Magma-Software wurden der Füll- und Erstarrungsprozess des Angusssystems und des Überlaufsystems der Frontabdeckung aus Aluminiumlegierung eines bestimmten Familienautomotors simuliert. Durch die Simulationsanalyse wurden die entsprechenden Probleme gefunden und das Programm zur Optimierung des Druckgussprozesses vorgeschlagen.
(2) Nach Ermittlung der relevanten Druckgussprozessparameter wurde der optimierte Füll- und Erstarrungsprozess erneut simuliert und die Temperaturfeldänderungen, Luftdruckänderungen und Erstarrungsbedingungen analysiert und zunächst die Sinnhaftigkeit des optimierten Schemas verifiziert.
(3) Um die Probleme der übermäßig hohen lokalen Temperatur und der langen Abkühlzeit von Gussstücken anzugehen, wird Hochdruckpunktkühlung verwendet, um die Abkühlgeschwindigkeit lokaler Bereiche zu beschleunigen und die Qualität der Gussstücke zu verbessern.
Komen